Think of the tools of a British coachbuilder. You’re probably imagining hammers pounding sheet metal or perhaps the hypnotic turn of an English wheel.
Now think again. At Britain’s only independent coachbuilder of new vehicles, it’s all about autoclaves to cure carbon fibre, 3D printers, and multi-axis milling machines to shape parts with nanometer precision.
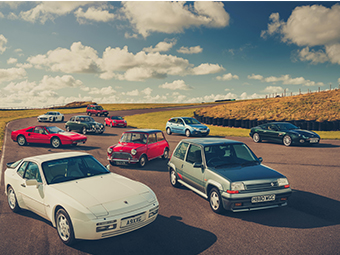
You won’t have heard of Allesley – at the time of writing the company didn’t even have a website up and running – but it is already working on bespoke commissions for wealthy clients, offering the kind of one-off vehicles that are beyond even OEM special divisions.
Allesley, named after a village just outside Coventry, the historical heart of coachbuilding, is a new venture from the people behind HPL Prototypes – who you probably won’t have heard of either. HPL has 25 years’ experience in building showcars and prototypes for the most prestigious brands, including Rolls-Royce, Bentley, McLaren, Aston Martin, Lotus, Jaguar, Land Rover, and Gordon Murray Automotive.
Its expertise in developing everything from clay models to running prototypes means HPL was uniquely positioned to fill the rapidly increasing demand for unique vehicles for individuals and also short runs for OEMs, and Allesley was formed.
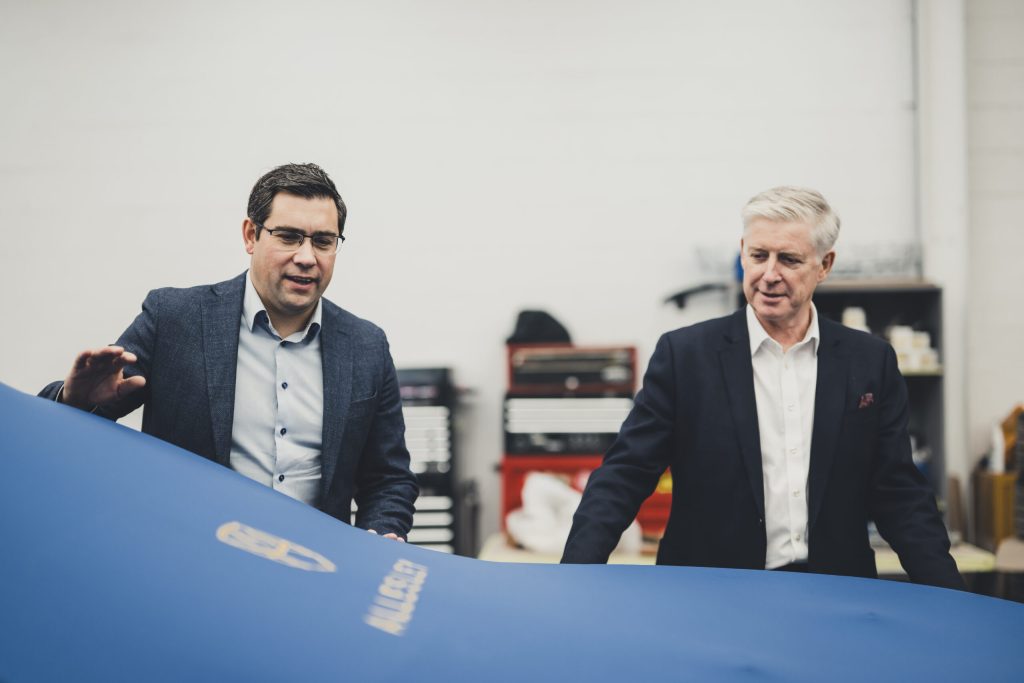
HPL CEO Chris Devane (above right) explains, “HPL’s reputation in supporting OEMs in the realisation of their project vision through bespoke concept design and prototyping is exemplary. However, HPL has – and always will – offer a solely commercial service. We have deliberately flown ‘under the radar’, majoring on confidentiality, because that is what our automotive OEM clients require. As we celebrate our 25th year, the time is right to launch Allesley which will draw on our world-leading expertise, and with a dedicated new team, bring to life bespoke vehicles for a new audience.”
“We’re not competition, we’re actually advocates for their brand,” adds Allesley CEO Paul Abercrombie (above left). “We’re making cars that individuals want that maybe the brands may not have the ability to deliver within their schedule, and with the capacity they’ve got.”
Unlike the first coachbuilders, Allesley have to work with a fully built vehicle, rather than a rolling chassis. Customers will need to purchase the donor car in their home country to ensure it meets local regulations before shipping it to the UK for the conversion – whatever form that may take.
It’s a collaborative process that can take years depending on the complexity. “It could take 12 months just getting out of the clients what they want, how they want it,” explains Abercrombie. “It requires a big investment of time from the client to give you the information required to get the best results. These are very busy individuals so it can be hard to be able to get time from them and it depends client by client. Having said that, we have a client at the moment who phones me every morning at 8am for an update.”
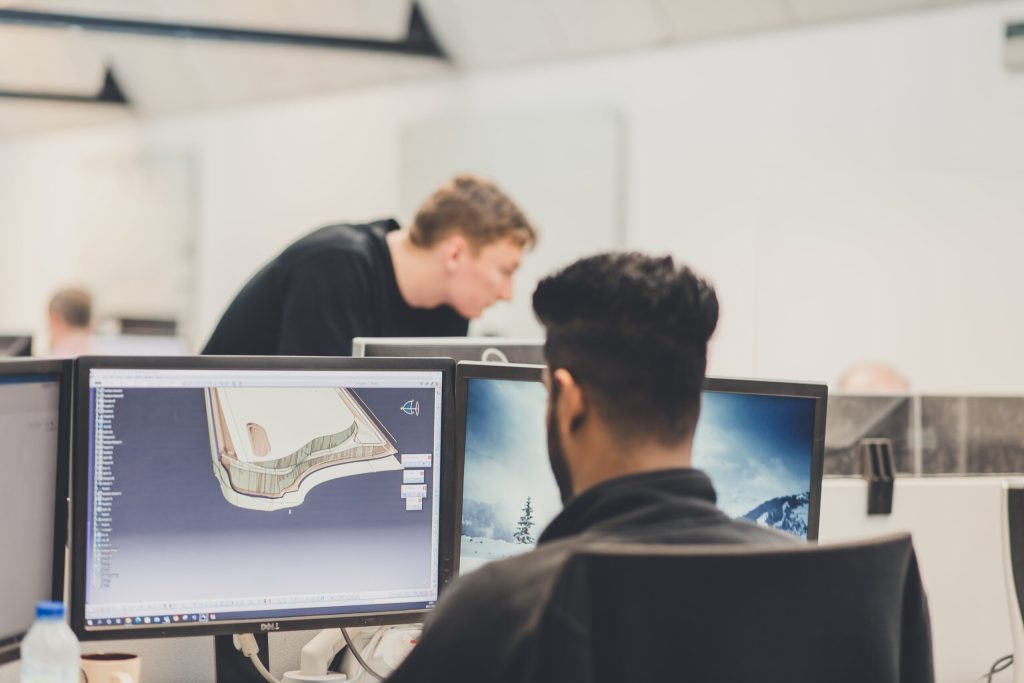
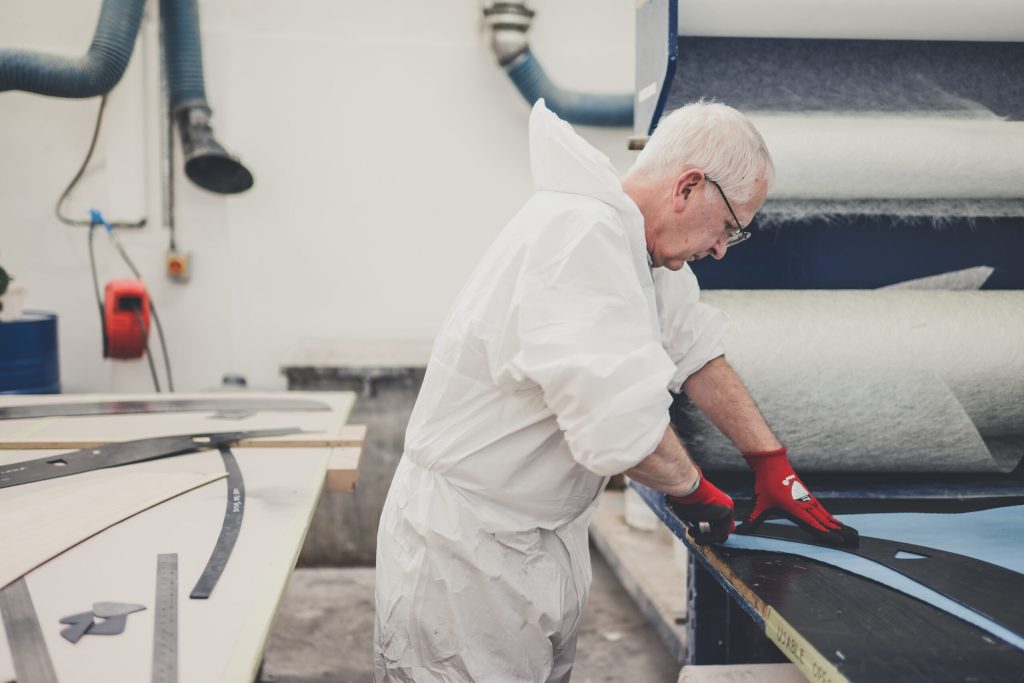
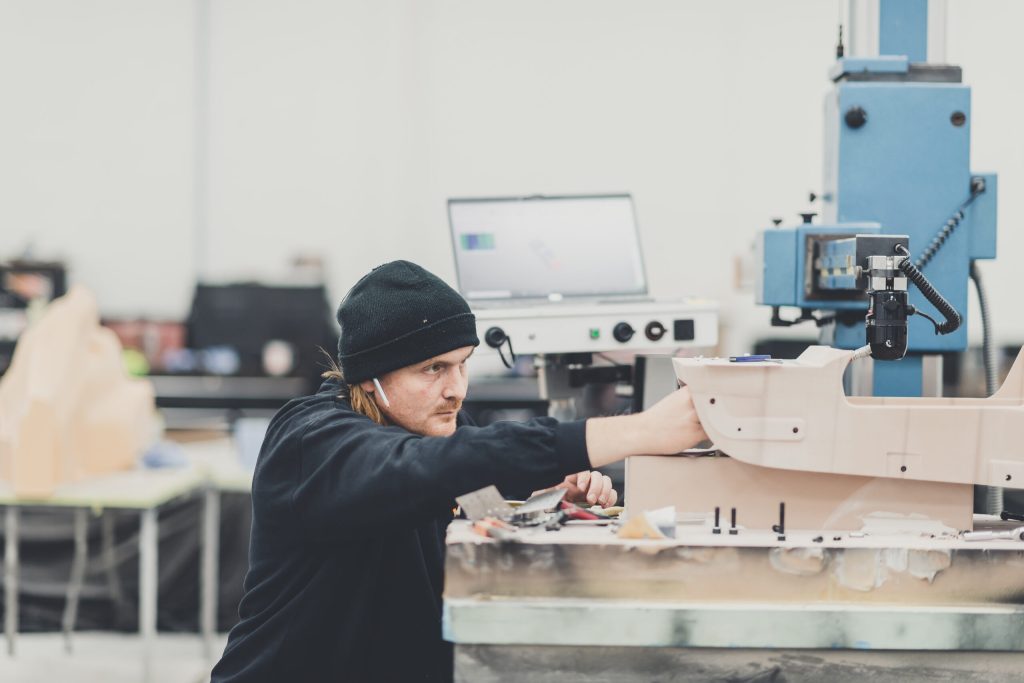
Clients have come to Allesley with a sketch, a full moodboard, and one even took away a clay model and had a go at sculpting it himself. “The actual developing of the car will be as much fun for the client as the car itself,” says Abercrombie.
During the development process Allesley is able to provide models – up to full scale – drawings, renders, and even virtual and augmented reality experiences depending on client preferences.
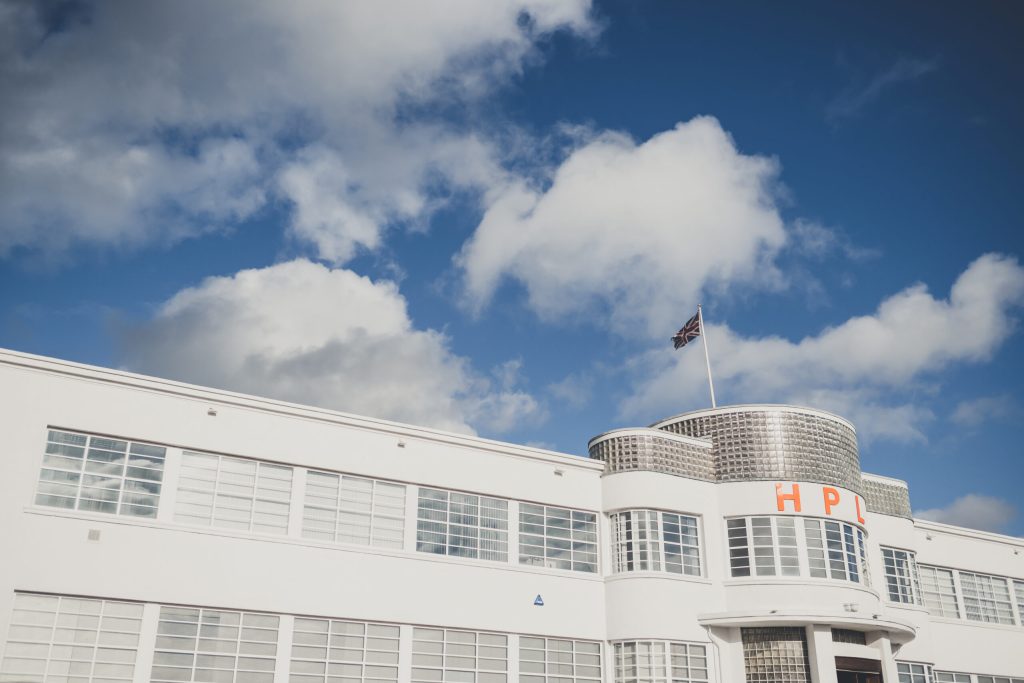
The firm’s fetching art deco facility, which once made parts for Spitfires and has a rich automotive history building racing Triumphs and the Rover SD1, can handle up to five bespoke builds at a time. A ballpark figure for a coachbuilt model is three to four times the cost of the new donor vehicle, but if extensive prototyping is required the numbers could run much higher.
“If someone wants to put a much more powerful engine into the car, for example, then the challenge will be is it usable power? Or is the chassis able to cope with the increase? Is it safe? What we’d recommend is that we would do a development program with a test mule, and that’s going to cost a lot more.”
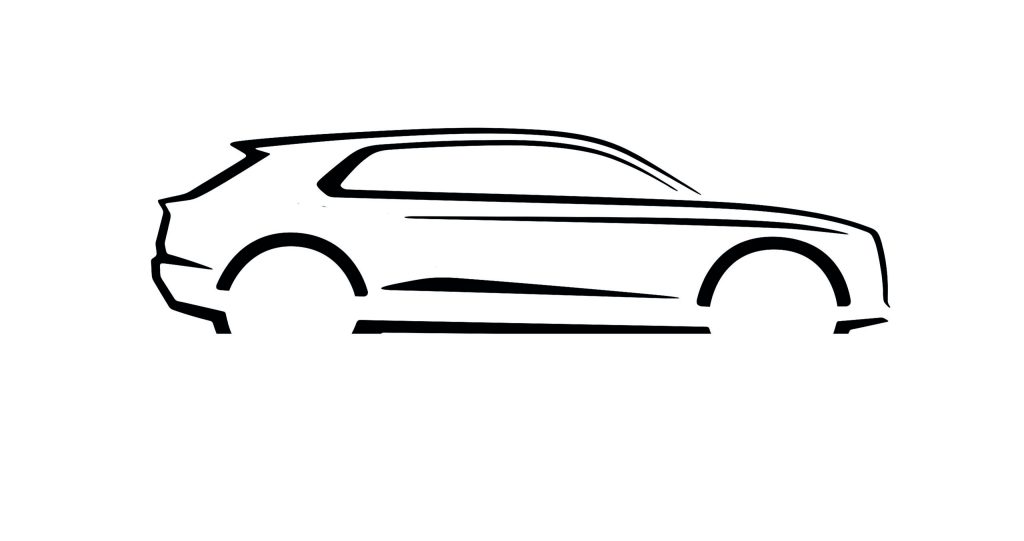
Allesley will reveal its first one-off customer car in 2024, a luxurious extended-wheelbase SUV with a conventional powertrain, but the firm is actively looking forward to electrification.
“The skateboard chassis have to be so strong because of the batteries. It means that the cabin and the body structure give you more freedom, and the ability to use composite panels, made in our own composite centre,” says Abercrombie.
No hammers required.
It’s great to see that this iconic art deco building, on the A45, is still being used for automotive purposes. It was originally the Standard Motor Company’s service department (1930s – 1960s). In the last few decades it has been occupied by freelance automotive design companies who, like HPL, were contracted by OEMs.
As a Brummie who spent most of my working life as an employee of Standard, Rootes/Chrysler/Peugeot, all based in Coventry, it gave me a thrill to read about HPL’s new ‘Allesley’ spin off.