As each of us progresses from rank novice, timidly swinging a ratchet with both hands, to a DIY superhero who can diagnose a non-running engine based entirely on an internet comment, we encounter projects that build skills and confidence. Some of those projects go exactly as planned. Others are surprisingly infuriating.
The second kind of project hides complexity at every step. It demands special tools you didn’t know existed and techniques often learned only by doing.
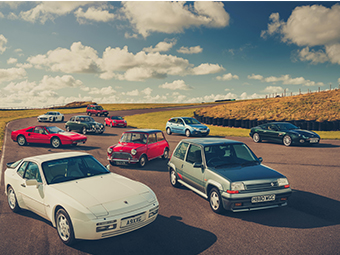
Haven’t run into these jobs? You’re lucky. Here’s a brief list of projects where, as they say, There Be Dragons. Consider yourself warned.
1. Building a roll cage
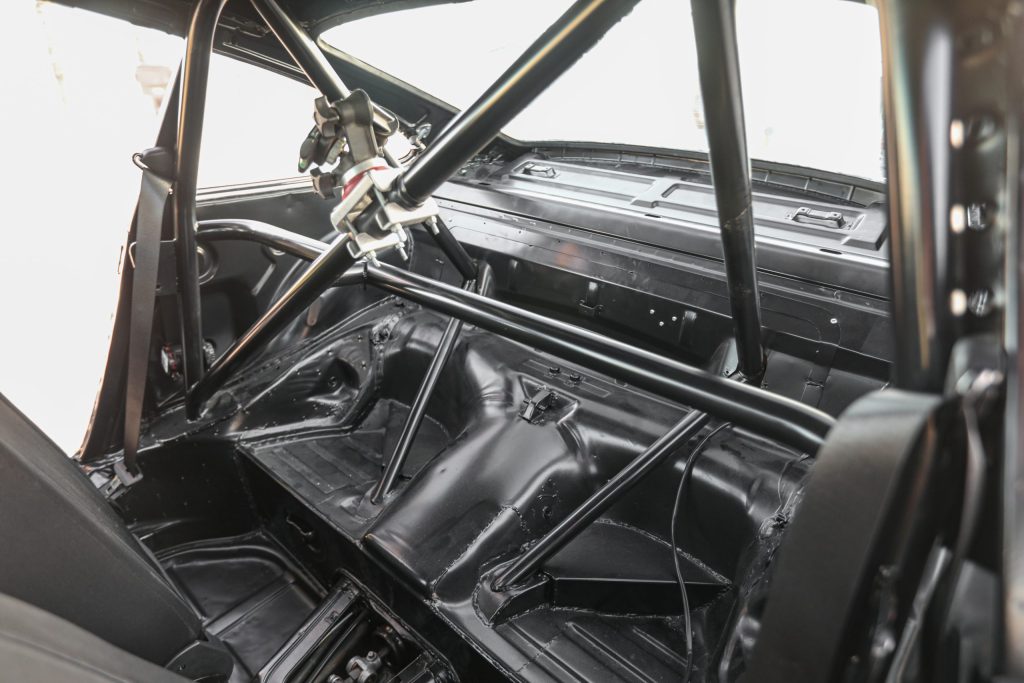
It’s just some welded tubes, how hard can it be? And yet, that isn’t the best attitude for building a device that might save your life. (Or, if you’ve done a really poor job, take it.)
A properly designed roll cage is just that – designed. Correctly tying a cage to a car’s body and/or chassis is critical if you expect the end result to have any safety value. This means deep consideration of things like tubing material, type, and thickness, but also the angles of those tubes and the placement of their nodes and footer plates. Geometry and load transfer are critical here, and with a roll cage, they hang on everything from tubing placement and bend radius to whether that floor supporting your main hoop will punch through in a roll-over.
Add in the required welds – they need to be structurally sound, with the right penetration and bead – and you have a complex recipe that can seem simple at first. If you don’t want the whole thing to turn into steel toothpicks when you need it most, educate yourself first. Or leave it all to a professional.
2. Sizing custom wheels
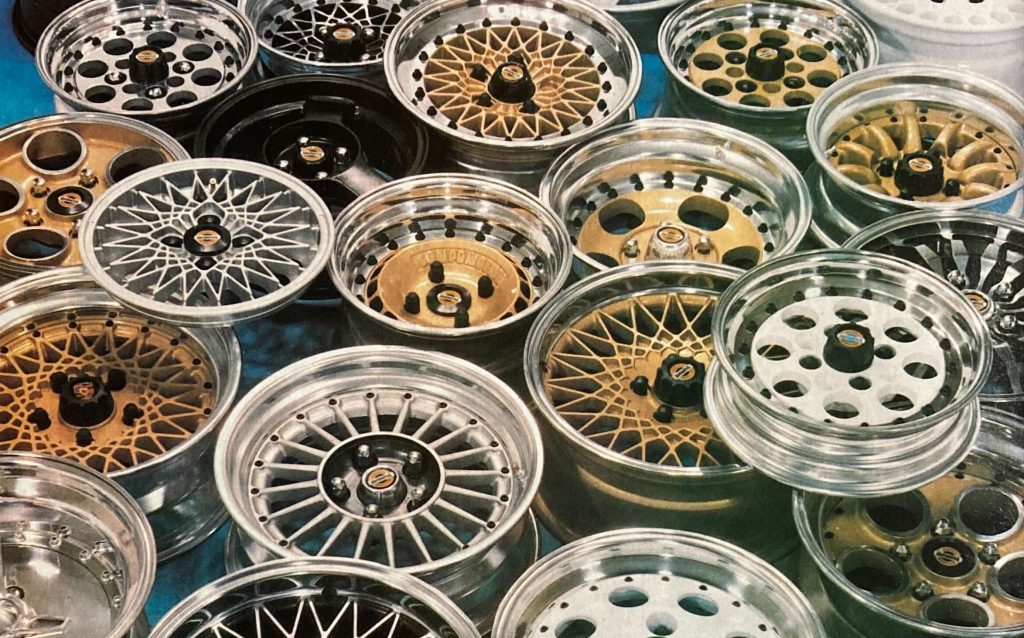
Loosen wheel nuts, remove wheel, bolt new wheel on, done. At least, if you’re lucky.
If you’re fitting truly custom wheels, you’re likely playing a game of measurement. A game that needs half a dozen reference points to really work. Wheel diameter, width, and backspacing are all variables in a system, and changing any of them can drastically impact a car’s steering response, handling, and ride quality. To say nothing of the clearance between wheel and tyre and body and suspension under full compression and full droop, or how the sidewalls deflect while cornering and what they might rub.
At the bottom of all this is the danger of conventional wisdom: wider tyres aren’t always better, a wider track isn’t always better, a shorter sidewall isn’t always better. There’s a lot going on.
3. Reassembling a differential
It’s only two gears, how hard can it be? Pretty hard, as it turns out. Hypoid gears, like those in automotive axles, are quite picky about lash – the amount of play between a pair of meshing gears, like a differential’s ring and pinion. Too much or too little and the gears will wear prematurely, or make noise, or even bind.
Add in the need to properly preload the bearing holding the pinion gear – some diffs make this harder than others – and you’ve got a complicated process. One that can cost a lot of time and money if you get it wrong.
4. Making an engine actually leak-free
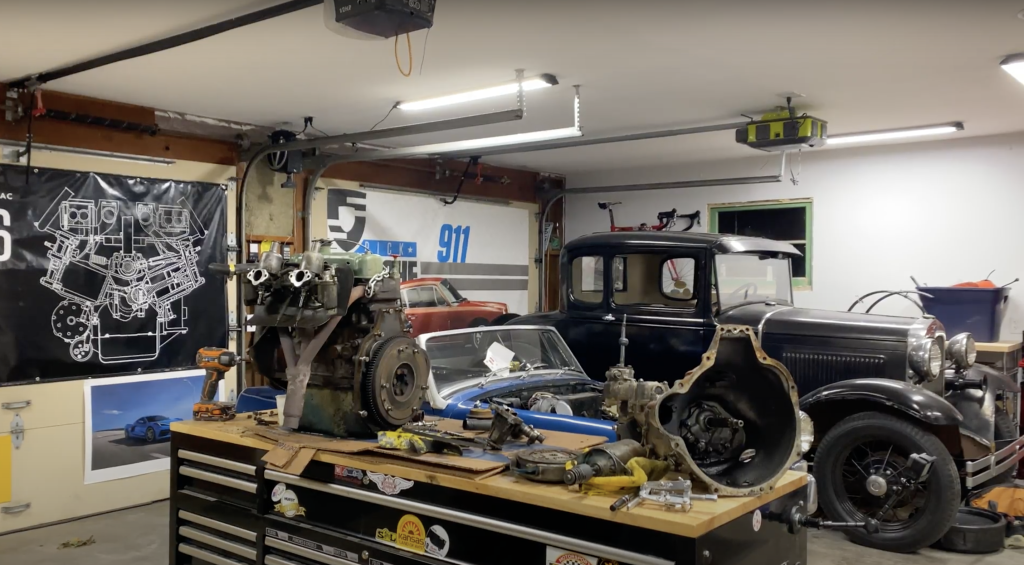
A multitude of factors go into this one. Machining. Surface prep. Cleanliness. The right chemical sealant. The right torque, the right fasteners. Using the right seals – sometimes that means a factory piece, sometimes not.
The older the engine, the harder it gets. Old-world solutions like cork gaskets, rope seals, and oil slingers conspire against you at every turn. That’s before you factor in gaskets and seals that might look identical to original parts but aren’t made as they once were. (Sometimes for better, sometimes for worse.)
Sometimes, modern materials can solve the problem. A dab of the right silicone or sealant might be all that’s needed. Other times, stopping a leak can mean using a hammer and a dolly to straighten an oil sump rail, or taking material off a warped manifold face to true it. Or even just having the self-restraint to not over-tighten bolts and crush a gasket too much.
If it was easy, all engines would be leak-free. And we know that’s not the case.
5. Headliners
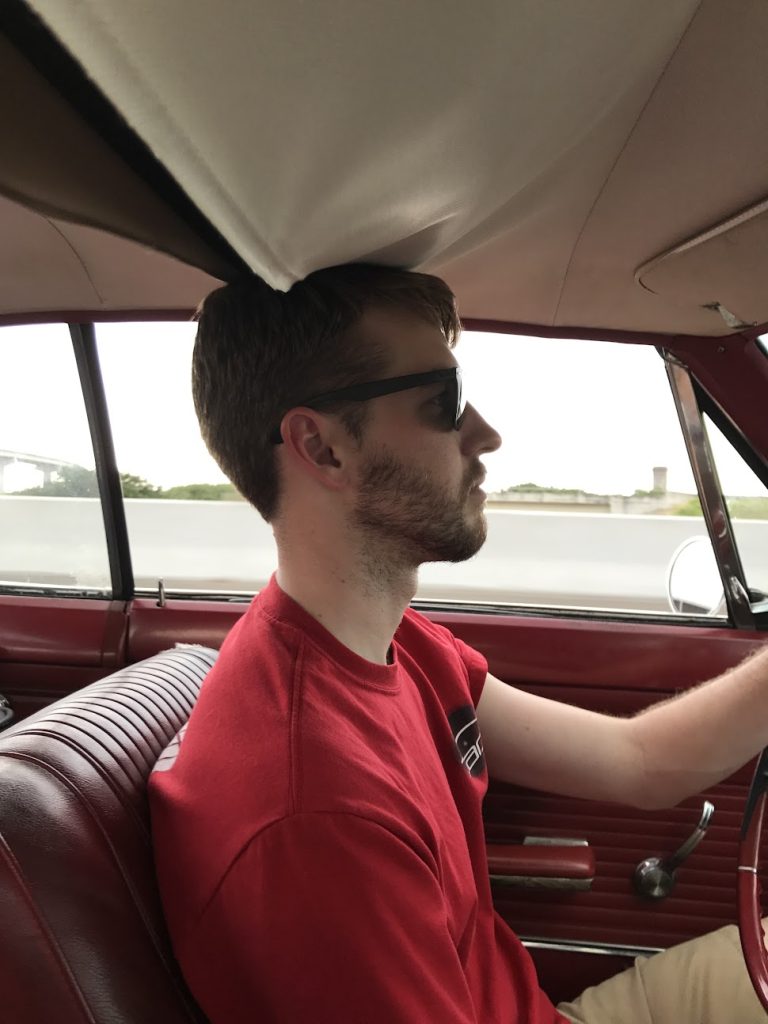
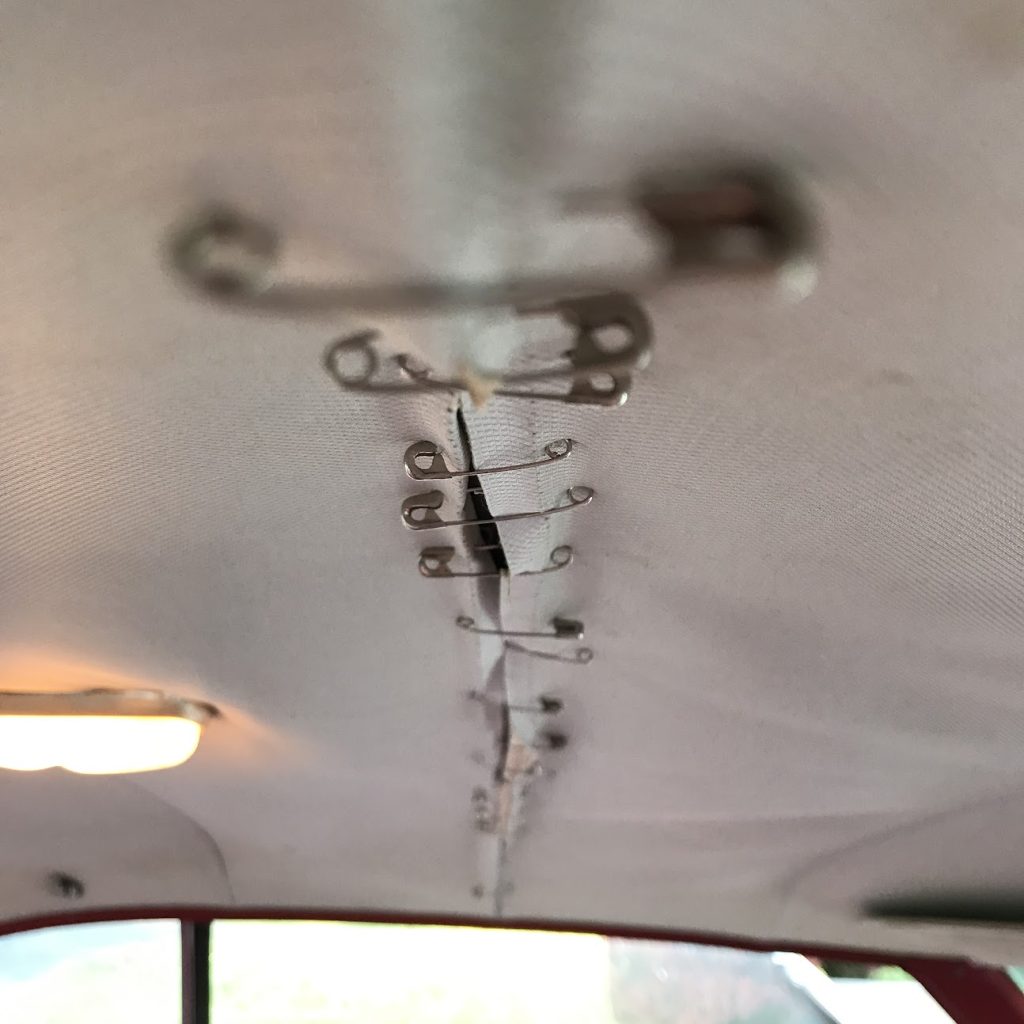
They’re the finishing touch on any interior but their position means that good work here is often overlooked. After all, a headliner lives above your head, and who looks up while driving?
A hung headliner takes a careful touch and careful planning to assemble. Bows must be tensioned at the right time, and any trimming of the headliner material must be judicious and careful. Cleanliness is paramount. Stretch the headliner’s various sections at the right time and in just the right direction, you won’t get wrinkles. Or, maybe the whole job goes perfectly, but a small mistake at the end forces you to start over and order new fabric.
“Headliners,” as Hagerty editor-at-large Sam Smith says, “are like building a ship in a bottle: Straightforward, if you know the tricks. And it looks like magic if you don’t.”
If you’ve never tackled it before, the job can be mysterious and frustrating. Even the one-piece moulded headliners of modern vehicles can be infuriating, as you never quite know just what, exactly, has to come out of the interior (sometimes it’s everything) simply to wrestle that large ceiling tray in or out of the car.
This article was originally published on Hagerty US.
Read more
11 winter project ideas for every skill level
Reviewed & Rated: All you need is gloves
Testing a tyre to the limit… unintentionally
… and strip/rebuild of a Hillman Imp gearbox in your girlfriends drive when you need the car to go to work the next day … a disintegrated cir-clip being the culprit … completed curtesy of Mr Haynes