In the hall of famous wheels, alongside the likes of BBS and OZ, sits the Rays TE37. A lightweight, strong, and six-spoke design that has stood the test of time, the TE37 is one of if not the pioneering design in the forged-wheel world. How does Rays create it? Thanks to YouTube, we got an inside look.
To start, we need to define a few terms. First, cast wheels. These are constructed by pouring molten metal into a mold, leaving the material to cool, and then finish-machining it into ready-to-install form. Forged wheels use a similar process combined with nature’s time-proven method of creating great things: pressure and heat.
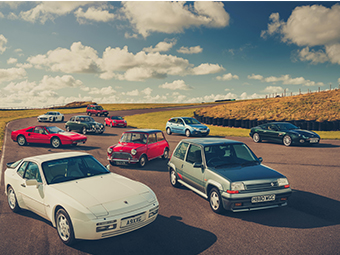
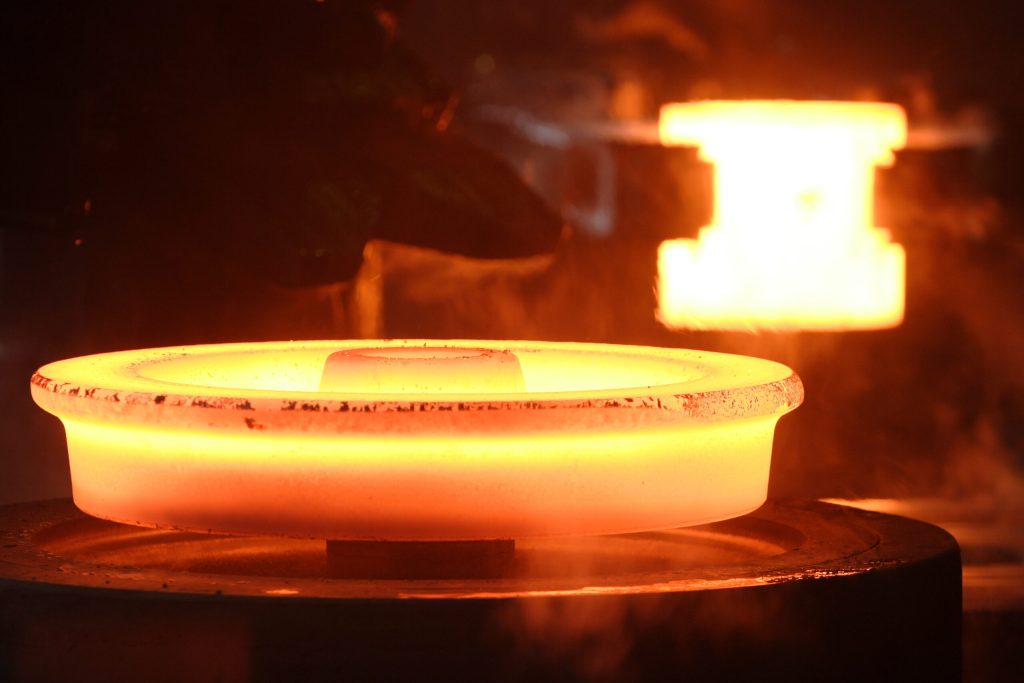
The initial three pressings of the raw material bring the face of the wheel into shape as a gigantic press applies several thousand tons of pressure. This incremental pressing refines the grain structure of the aluminium, making the end product stronger and less fragile than a cast wheel.
However simple the process may sounds, multiple points in this video confirm that Rays wants to keep some trade secrets, well, secret. There is a lot more to the exact process than just clamping some aluminium in a huge press – and we do mean huge.
A home shop press might be capable of producing ten tons of pressure; the one used to create TE37 wheels is capable of producing 10,000. That’s why, after only a few seconds, you can recognise that classic six-spoke design in what used to be a round chunk of slag.
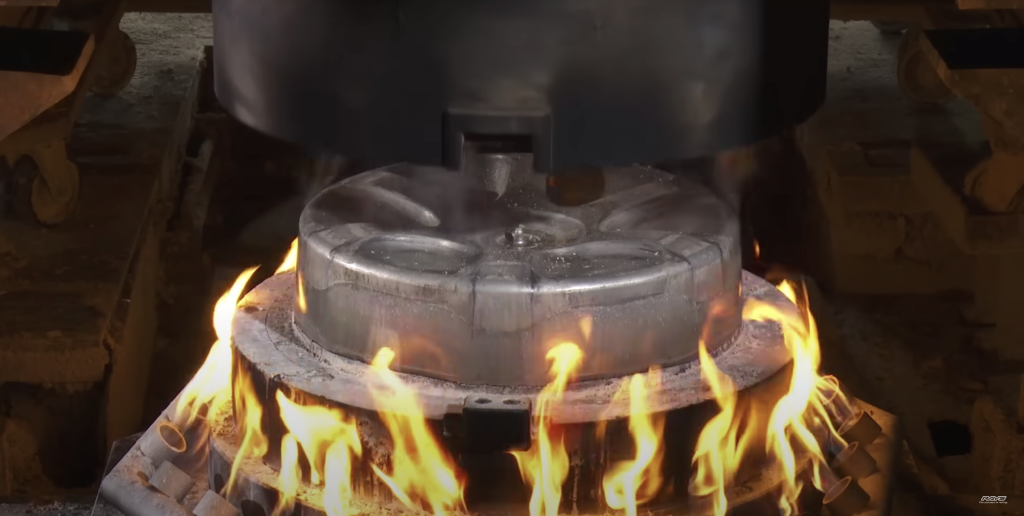
Once that wheel face has been pressed into rough shape, the edges are rounded to make it safer to handle and to keep fractures or bends – known as stress risers – at bay. The final shape is so much more than meets the eye, even if it still doesn’t look like a wheel. That milestone is reached when a pair of rollers push what looks like excess aluminium down and around to create the barrel of the wheel.
From there, the wheel goes off to heat-treating and finish-machining. The first process hardens the wheel, and the second trues up the mountain faces and adds recesses for the lug nuts. After a little pop of color, the wheel heads to the tire shop for some rubber.
A lightweight forged wheel is still the gold standard, even as carbon fibre wheels become increasingly popular. (You can find woven rims on dealer lots these days.) Forged aluminium has strength and durability of which a carbon fibre wheel could only dream: If you drive pot-holed streets or take a little too much kerb during on-track excursions, we can probably guess what your wheels are made of. A wise choice, and now you know exactly how your wheels went from raw aluminium to race-ready.