To mark the 150th anniversary at the Audi site in Neckarsulm, Germany, a dozen apprentices at Audi completely overhauled an iconic classic car into a modern EV.
On 8 July, the trainees from the automotive mechatronics, bodywork, and vehicle construction and painting courses proudly unveiled the ‘EP4.’ The ‘E’ stands for electric drive, and the ‘P4’ for the NSU Prinz 4, a model produced in Neckarsulm by NSU Motorenwerke from 1961 to 1973. The car was unveiled at an Audi corporate gathering called Family Day.
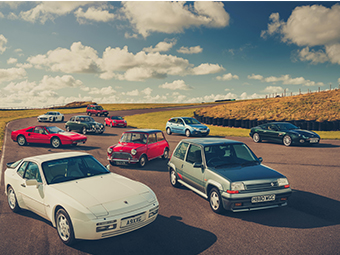
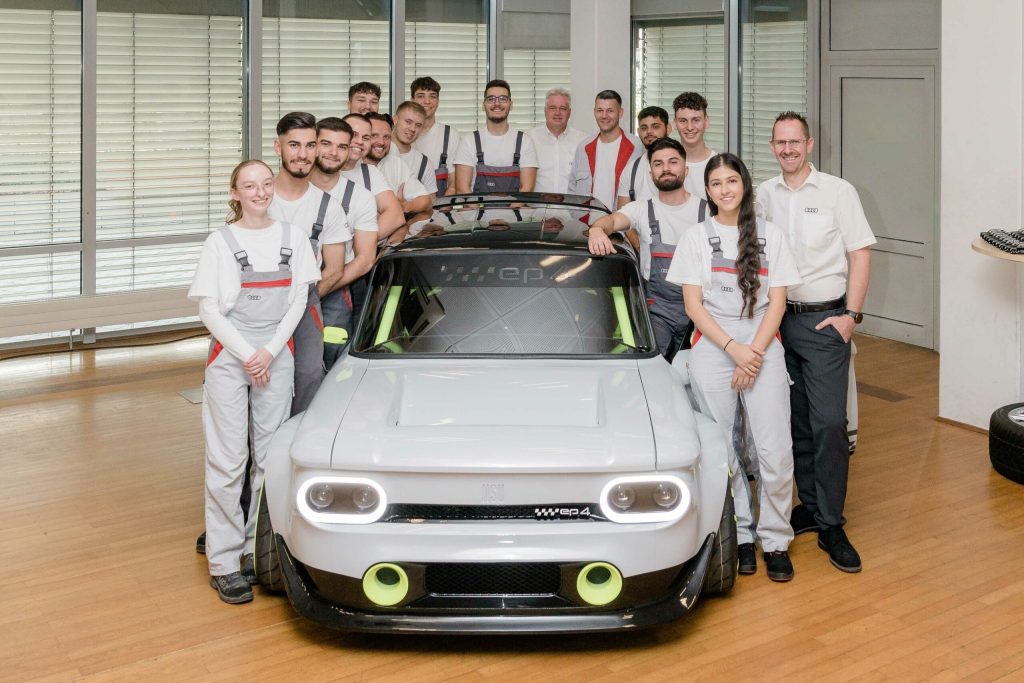
“We wanted to build a car that was not only fast and looked cool but also honored the 150th anniversary of the site,” says Dean Scheuffler, an apprentice automotive mechanic at Audi in Neckarsulm. The starting point: an NSU Prinz 4 built in 1971, which had been off the road for decades until its resurrection in January 2023. “The apprentices awoke this ‘prince’ from its slumber and fitted it with a new high-voltage heart,” Audi said.
But it was a long road from the project launch in January to the big reveal at Family Day. In numerous team meetings, trainees, trainers, and project managers exchanged views on the project‘s challenges. The first task was to create a solid foundation for the conversion. Mizgar Doman Hassan, an apprentice bodywork and vehicle construction mechanic, said, “When we got the car, its body had several rust spots. These areas were the first thing we fixed.”
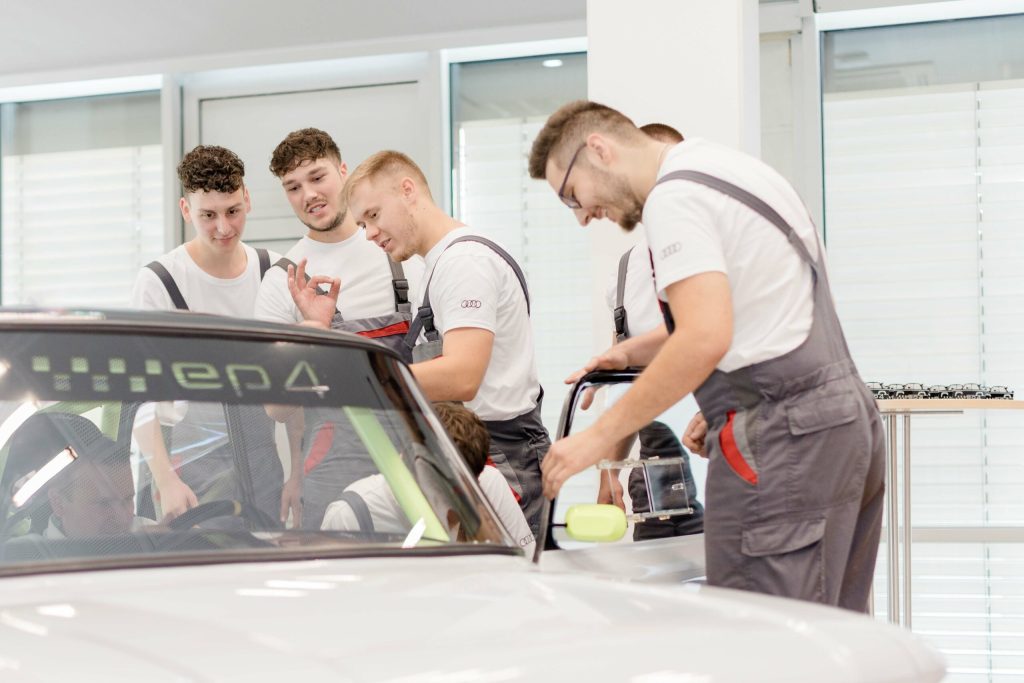
While the budding body and paint specialists tackled the classic car’s chassis and outer skin, the future automotive techs got to work on the powertrain, battery, and suspension. The rear of the Prinz, where a two-cylinder petrol engine with 30bhp once lived, is now home to a 240bhp (176 kW) electric motor. It comes from a 2020 Audi e-tron and gets its power from a battery originating in the plug-in hybrid Audi Q7 TFSI e Quattro.
The battery sits under the bonnet, where the NSU Prinz once had a fuel tank. The electrified machine breathes through a wide air intake at the bottom of the bumper, while heat can escape through a large opening in the front lid. The tailgate also improves cooling and can be fixed in a half-open position. “Thus, it reveals the electric power plant and is reminiscent of historic racing cars based on the sporty NSU Prinz 1000. Where a row of open carburetor funnels gave onlookers clues about the sporting intentions of these cars back then, the EP4 now displays its electric motor.”
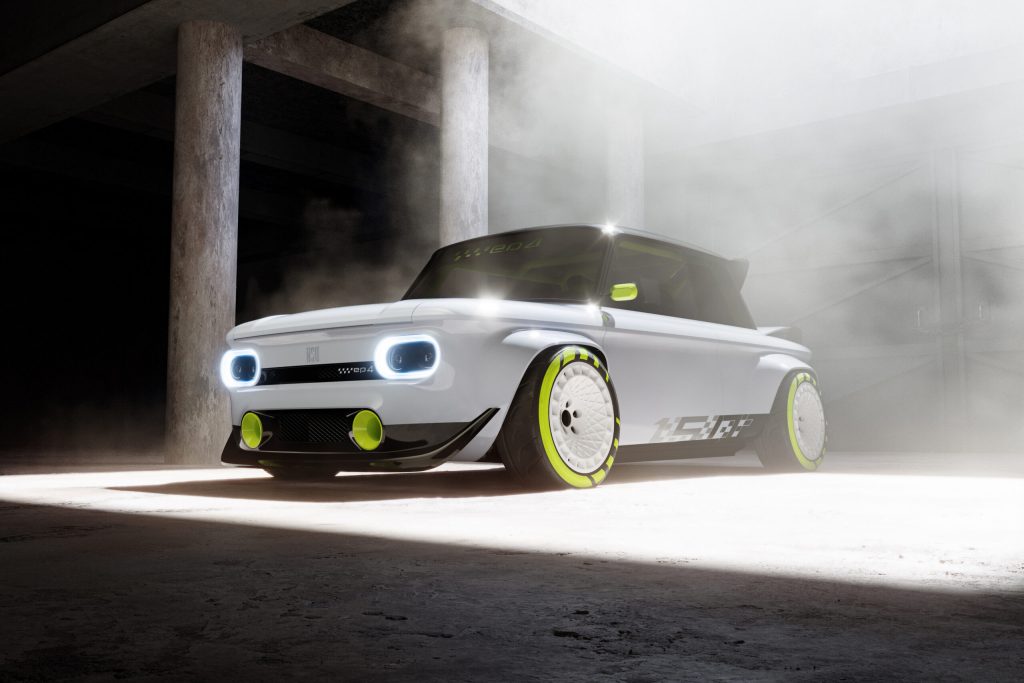
For the apprentices, it was clear that their EP4 should show that it began life as an NSU Prinz. The historic elements, therefore, include not only the front and rear lights. The body from the 1970s also retained its characteristic shoulder and roof lines. The apprentices eliminated the rust and painted it in Audi colours – Suzuka Grey and Brilliant Black. Accents such as the anniversary lettering “150” were applied to the side of the vehicle.
The big leap in performance required extensive modifications to the chassis and the bodywork. A modified floor pan from an Audi A1, including brakes and axles, forms the base. The apprentices mounted the extensively-altered and significantly-widened body on top. “The muscular fenders are unmistakably athletic,” Audi said. “The apprentices designed these with the support of Audi Design and turned them into reality using 3D printing. Wide wheels are tucked beneath the fenders. Thanks to modern performance tyres, they provide the necessary grip during acceleration and sporty cornering.”
“We wanted the EP4’s performance to be visible from every angle,” explained Cynthia Huster, apprentice automotive painter. The rear wing, painted Signal Yellow, gives the EP4 a particularly sporty appearance. The twist: The wing is not attached to the bodywork, as in other vehicles, but to the roll cage. Its supports, therefore, go through the rear window.
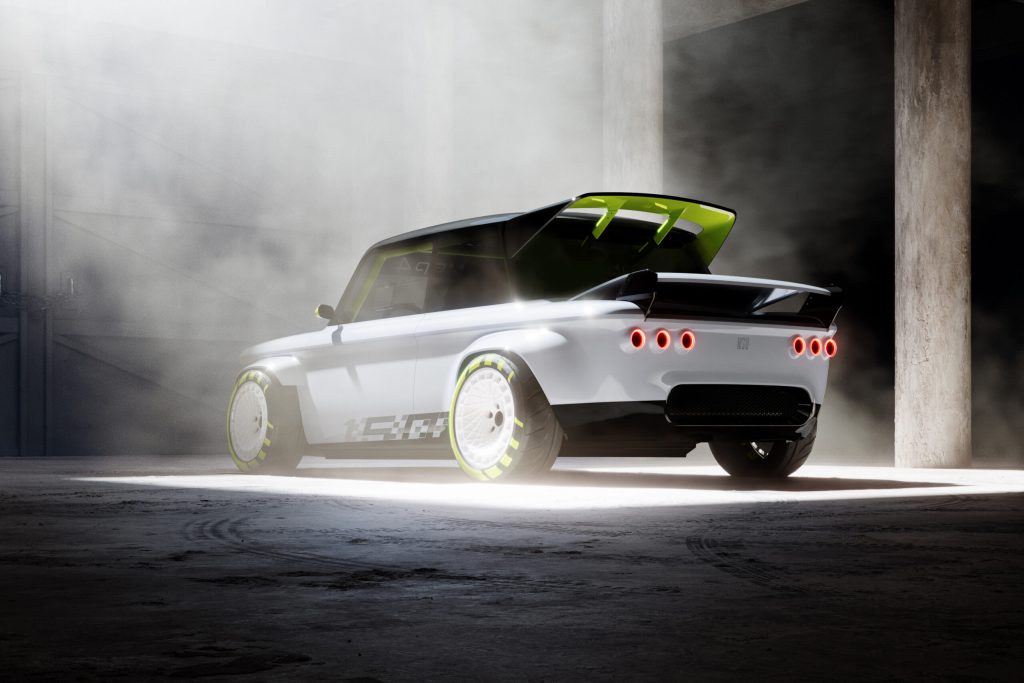
The Signal Yellow roll cage makes for an eye-catching contrast in the interior. Apart from that, the interior – typical of racing cars – is reduced to the essentials; all other painted surfaces are black. The occupants sit on Recaro Podium bucket seats. A computer and corresponding screen serve the instruments and displays.
In all the steps, the trainees put the knowledge they had acquired during their training to practical use. Timo Engler, Head of Training Vehicle Technology/Logistics, said, “The project gave our apprentices a chance to work freely with different techniques and materials. For example, in addition to the electric drive, they used 3D printing, a second technology of the future. Carbon fibre – familiar from motorsports – was also used for the front hood.”
Audi board member for human resources Xavier Ros was impressed with the unique project. “With admirable commitment and considerable creativity, our apprentices have built a tremendous car. They can be really proud of the result,” said Ros.