The arrival of Tesla’s cheapest car will herald a new era for car production, claims a report in Car magazine.
The compact Model 2 has a target price of £25,000 and to keep build costs down Musk’s engineers have devised a whole new way of building it. Instead of a traditional production line, invented over a century ago by Henry Ford for the Model T, Tesla will use a method it calls “unboxing.”
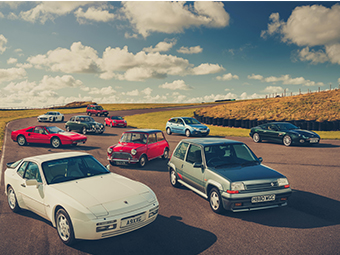
Rather than the car gradually being built up as it progresses along a line, Tesla plans to use a series of sub-assemblies which then come together at the end, made possible by the company’s “megacast”platform. The rear megacast, for example, would have wheels, seats and drive unit fitted, with the front seats and center console installed on top of the battery pack. The various part-built sections would then be united to form a complete car.
Under this method Tesla is targeting a 50 per cent reduction in cost, largely because the process requires fewer workers. The process would also reduce the manufacturing footprint by 40 per cent.
Reinventing the production process is necessary because, as a car works its way down a conventional production line, “Most of the time we’re doing nothing to it,” says Tesla’s head of vehicle engineering Lars Morvay.
The first Tesla factory to deploy the unboxing production method will be the Giga Texas plant in Austin which is currently outputting the Cybertruck. Car states that some of the Cybertruck’s tech will make it into the budget model, including its 48-volt electrical architecture and drive-by-wire steering. Batteries will be the 4680 units which are used in the Model Y, and a new motor will be built without the use of rare earth metals, saving further expense.
Car doesn’t provide a timeline, which given Musk’s propensity for delays, is probably wise. We won’t be holding our breath.