You’d almost swear that the people who design and engineer cars never work on them. Sometimes you’re left swearing at the people who created a part of your car, scrambling to understand the logic of why the bolt had to go there. Yes, there, deep between a rock and a hard place – or more accurately, the engine and frame rail, or any number of impossibly tight squeezes, such as when refurbishing suspension.
In either case, the game of floating a bolt on the end of a socket can sometimes be the only way to install it, with access for any normal human hand limited by the confines of a mechanical labyrinth. If that sounds familiar, and you’re dreading getting stuck into to a maintenance task, here are three simple ways to make life easier when launching into the abyss of any maintenance project. Good luck.
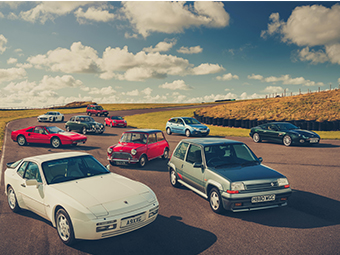
Grease the bolt’s head
A tub of axle grease is one of the most useful automotive products you can buy, and its high viscosity and stiction make it a great temporary “glue” for a socket and bolt. Spread a small glob on the head of the bolt to keep it in place, and once it’s installed, use brake-clean or a degreaser to clean the grease off so that it doesn’t collect dirt.
Wrap it in tape
Even a 14mm bolt can even be dangled from a 15mm socket with enough laps with a strip of tape, so vary the thickness as needed. Photo by Phillip Thomas | Hagerty Media Site
For the bolt to be loose in a socket, there has to be some gap between the two pieces that allows for it to slip out, right? A few laps with a piece of tape over the head of a bolt can build up a little more diameter, and wedge it into the socket. Once it’s home in its hole, just grab the tape and rip it off. Duct tape is the obvious choice here, but masking tape will fall off with no mess.
Invest in a magnetic socket or make your own
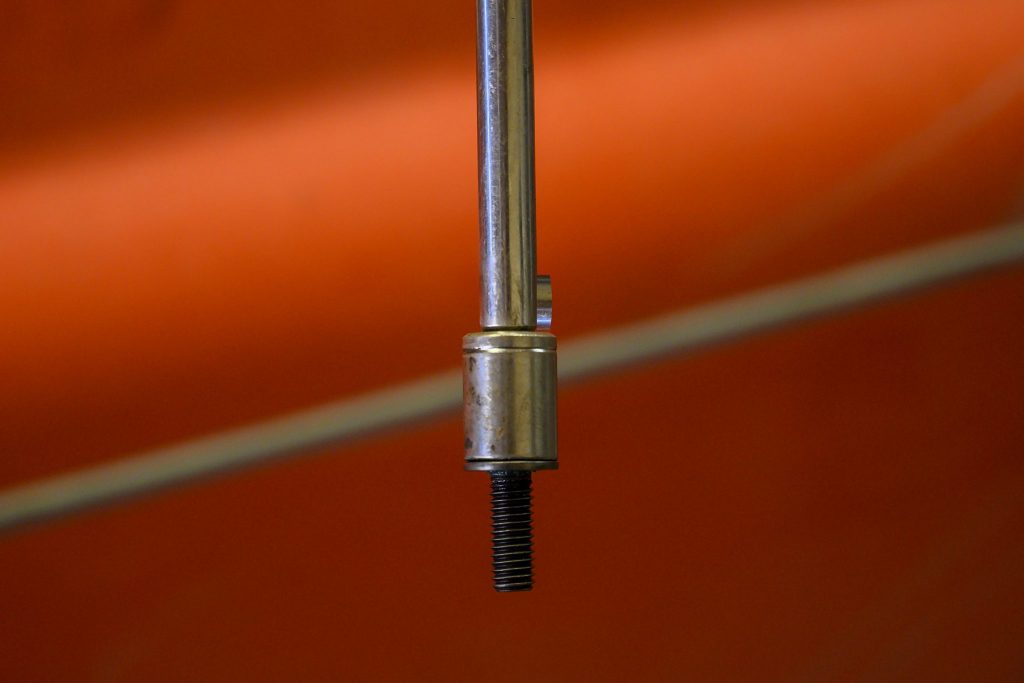
Seems obvious, and many specialty tools already use them, but sticking a rare-earth magnet onto your socket or the extension itself can magnetize the whole assembly. You can buy neodymium magnets online, or if you have an old computer hanging around, the old-school mechanical hard drive can be torn apart to salvage the half-moon shaped magnets that the actuator arm uses to drive itself across the platters inside, like the tone arm of a record player. The downside to this method is that the magnet can be knocked off or fling itself onto another metal part — but, it’s one of the strongest methods to snake a bolt in.
Need to free a suck bolt? Loosen up DIY with WD-40, AC-90, Bilt-Hamber and GT85. Which is best?