The factories that create the cars we see on the road are slight mysteries to most enthusiasts. Sure, we know there is a building somewhere with a bunch of parts that get assembled into a functional object, but what does that actually look like? If you are interested in the cutting edge of performance and engineering, more often than not you are left a little high and dry. Until now.
In a video released on the Koenigsegg YouTube channel, the founder himself – Christian von Koenigsegg – takes us on a quick walk through the assembly area where the Jesko’s nine-speed, seven-clutch transmission is assembled. The parts look downright absurd to anyone who has spent more time under the bonnet of a car than staring at a computer screen running a CAD program. Looks aside, however, all of these parts have cousins in the “regular” car world – on the high-performance Jesko they’re just dialed up to 11.
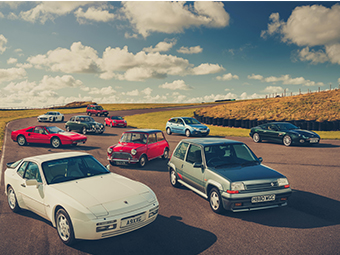
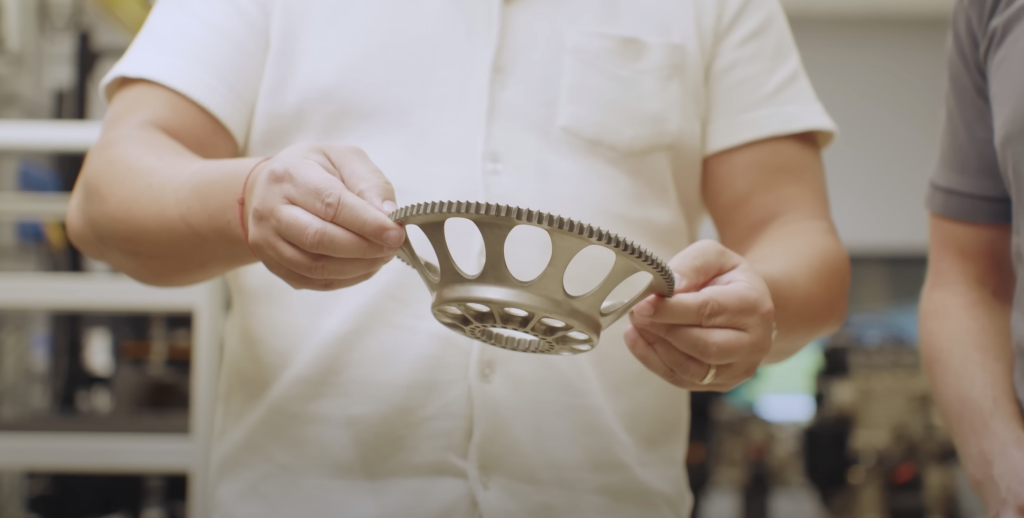
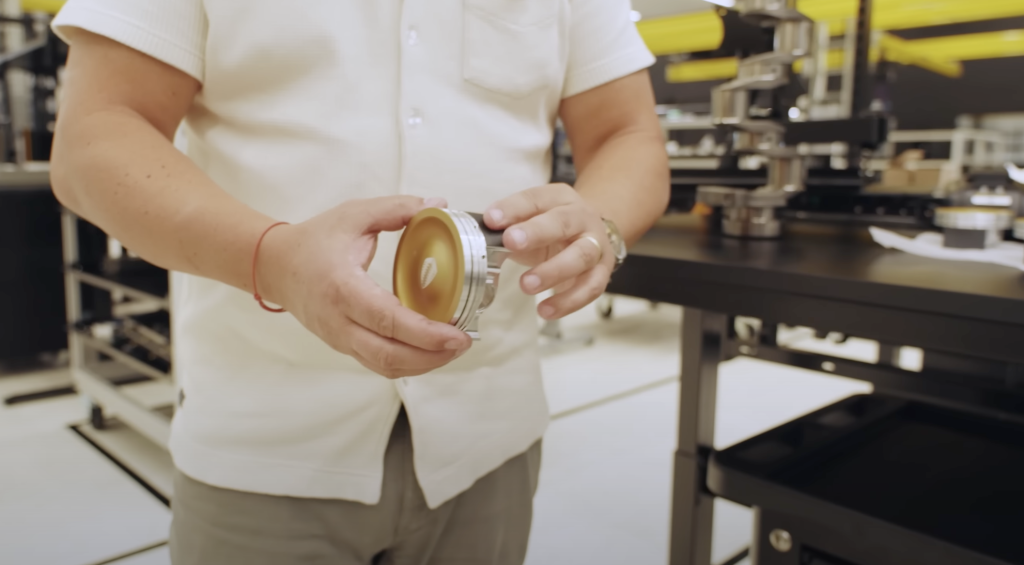
The starter gear for the Jesko is a prime example. Rotating mass is the enemy of quick-revving engines, and the flywheel is typically one of the heavier parts of an engine’s rotating assembly, right up there with the crankshaft. Christian points out that the Swiss-cheese–looking starter gear is actually the largest diameter metal part in the drivetrain. Considering how easily he flips it around with one hand it becomes clear why the Jesko’s 5-litre V8 revs so quickly.
Next step on the tour is the engine assembly, just steps away. Here one technician builds one engine per week. Seeing the pistons and crankshaft on the table is one thing, but seeing a completed engine and just how compact the whole package is – that’s something else entirely. The crankshaft is extremely svelte, while the connecting rods provide a beefy counterpoint. Pistons are coated both on the crown and the skirt to reduce friction and help with thermal management.
Then it’s off to the dynamometer, because of course Koenigsegg has an in-house engine dyno. Christian talks with the dyno operators to give a brief look into what kind of measurements they are looking for as new engines are developed and run before going into production. Some tuners might only look at spark plugs and air-fuel ratio, but naturally there’s more to take into account when extracting in excess of 1200bhp from just five litres of displacement.
It’s a stunning place for sure, but it is also easy to see why few cars can be built this way. “It’s really like Swiss watch manufacturing, in a way,” Christian tells us, “but on a larger scale.” That sort of astronomical precision comes with a price tag, of course. So much of modern automotive production is based in compromises for efficiency, time, and serviceability. This sort of behind-the-scenes tour allows us to see what can be built when those restrictions are thrown out the window.